1. IEPE Introduction
IEPE refers to an acceleration sensor with a built-in charge amplifier or voltage amplifier, also known as ICP by some.

This name originated in the 1960s and 1970s. At that time, many manufacturers produced piezoelectric sensors with internal circuits. Among them, the company PCB named its sensors ICP, and other companies also began using this name.
As the market expanded, PCB registered ICP as a trademark, making it unavailable for other companies. Therefore, the industry proposed the name IEPE for such sensors, which has gradually gained recognition among many companies in the industry.
2. The measurement principle of IEPE
Since IEPE is a piezoelectric sensor, it naturally utilizes the piezoelectric effect. The piezoelectric effect is divided into the direct piezoelectric effect and the inverse piezoelectric effect. Specifically, IEPE utilizes the positive piezoelectric effect.
The direct piezoelectric effect means: when certain dielectrics are deformed under external force in a specific direction, polarization occurs inside the dielectric, generating opposite positive and negative charges on its two opposite surfaces.
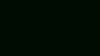
When the external force disappears, the charges vanish. When the direction of the external force changes, the polarity of the charges also changes.
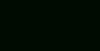
IEPE is also an acceleration sensor. How does it convert acceleration into an electrical signal?
Acceleration is defined by Newton’s second law: the magnitude of an object’s acceleration is directly proportional to the applied force and inversely proportional to the object’s mass. The direction of acceleration is consistent with the direction of the force.
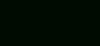
In the formula, “F” is the resultant force on the object, “m” is the object’s mass, and “a” is the object’s acceleration, with the unit m/s2. The mass “m” generally does not change and can be measured in advance. The magnitude of force “F” can be measured using the piezoelectric effect, allowing the calculation of the object’s acceleration.
3. The structure of IEPE
IEPE is integrally assembled in a metal shell, with a base of high stiffness connected below. Inside the shell, two piezoelectric sheets form a piezoelectric element with silver-plated surfaces. A metal sheet between the piezoelectric sheets transmits, the charges generated by the piezoelectric element to the integrated circuit through leads. Above the piezoelectric sheets is a mass block with low mass, which is preloaded by a spring or bolt with high stiffness.
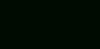
When using IEPE to measure vibration, the sensor should be fixed to the measured object. Due to the high rigidity of the spring and the low mass of the mass block, the vibration experienced by the mass block is the same as that of the base. Due to the continuously changing inertial force of the mass block, the pressure on the piezoelectric sheets changes continuously, generating high-impedance charge signals. These charge signals are input into the built-in integrated circuit through leads connected to the metal sheet. The integrated circuit then converts the input charge signals into low-impedance voltage signals for output.
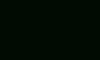
IEPE also requires a constant current source for power supply, with a current generally between 2mA and 20mA. In most cases, a constant current value of 4 mA is a good compromise, and the supply voltage is between 18V and 30V. The sensitivity unit of IEPE is mV/g, where g is the gravitational acceleration. Higher sensitivity means a smaller measurement range, while lower sensitivity means a larger measurement range. The maximum range of the sensor is determined by the ratio of the maximum output voltage to the sensitivity. When selecting a sensor, these two parameters require special attention.
4. Collect vibration information of the fan using a collection card
Next, we use a data acquisition card to collect the acceleration information of IEPE and simulate the vibration information change when an object is damaged using a fan.
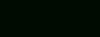
The experiment requires: USB-3213 data acquisition card, SRD-1104-IEPE signal conditioner, IEPE sensor, and fan.
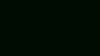
The SRD-1104-IEPE signal conditioner can adjust the IEPE polar signal to a bipolar signal, and provide a 4 mA constant current power supply for the sensor. The conditioner can be powered by USB or an external 24V power supply. Relevant parameters of IEPE range 10g, excitation current 2mA–20mA, sensitivity: 501.5 mV/g.
Next, connect the experimental equipment: Connect the IEPE sensor to the IEPE 0 interface of the signal conditioner; connect the IEPE OUT 0 interface of the IEPE signal conditioner to AI 0 of the acquisition card; connect GND to AI Sense of the acquisition card; short-circuit AGND and AI Sense on the acquisition card.
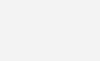
Then connect the acquisition card and the signal conditioner to the computer via a USB cable; finally, fix the IEPE sensor on the fan frame.
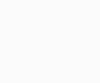
Before collecting data, set up the software: Set the vertical coordinate to -10 to 10, and uncheck the automatic coordinate adjustment.
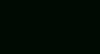
In the software settings, check the single-ended mode.
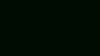
Check the AI 0 channel.
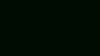
Set the sampling rate to 10k.
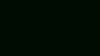
Check the unit change to make the sensor output voltage range from -10 to 10, with the sensor unit as “g”, and the sensor range set to -10 to 10.
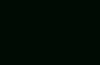
Select the data storage path.
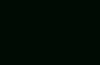
Keep other settings unchanged. Finally, set the horizontal coordinate to 0–100.
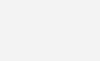
Click start. When the fan does not rotate, the vibration basically does not occur, and the data stabilizes at the 0 coordinate.
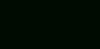
When the fan rotates normally, the data fluctuates between 0.2 and -0.2.
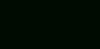
To simulate fan damage, paste a paper ball on the fan blade to disrupt its structure. When the fan is turned on, significant changes in its vibration information can be observed.
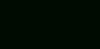
By observing the vibration data before and after the fan damage, it is easy to determine whether the fan is damaged.
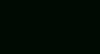
Open the data storage path. For easy viewing, convert the data to CSV format through software.
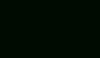
Open the file, and all the data collected in the experiment can be viewed.