What is RTD thermal resistance? The full name of RTD is ”Resistance Temperature Detector”. So to be precise, It should be translated as “resistance temperature detector”
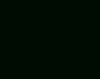
In the following, we will introduce RTD from four aspects.
1. Measurement Principle
RTD measures temperature by utilizing the property of metal resistance increasing with temperature. Why do metals have such a characteristic? It is because metals have a small number of outer electrons and are prone to lose electrons.
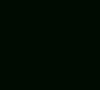
When a large number of metal atoms gather, most of them lose their valence electrons (outer electrons).
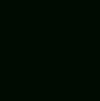
At this point, positive ions will arrange themselves in a certain geometric form and perform high-frequency thermal vibration at fixed positions, while the lost electrons become free electrons and move among the positive ions, resulting in good electrical conductivity of the metal.
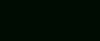
However, when the temperature of the metal rises, the thermal vibration amplitude between positive ions increases, hindering the movement of free electrons, leading to an increase in the metal’s resistance.
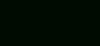
2. Common Types of RTD
Not all metals are suitable for use as measuring resistance. After screening, platinum, copper, and nickel are chosen as the materials for RTD. Platinum has stable and corrosion-resistant characteristics, and it does not undergo physical or chemical changes due to high or low temperatures.
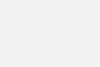
Therefore, platinum RTD is the most accurate and stable method for measuring temperature and is widely used in industrial production. Common models include PT100, PT500, PT1000, etc.
Nickel is a hard and ductile metal that is relatively corrosion-resistant.
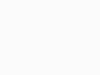
However, prolonged use of nickel metal accelerates aging and affects measurement accuracy, limiting the application range of nickel RTD.
Copper is a relatively soft metal with good ductility and conductivity.

At a certain temperature, the linearity of copper’s resistance-temperature relationship is good. However, copper undergoes oxidation at high temperatures, affecting accuracy, so copper RTD is more commonly used in low-temperature scenarios.Common models include Cu50, Cu100.
What do these RTD model numbers mean? Taking PT100 as an example, PT indicates that it is a platinum resistance, and 100 indicates that its resistance value at 0℃ is 100Ω. Other model numbers follow a similar naming convention.
3. Advantages of RTD
So what are the advantages of RTD?
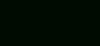
From the chart, it can be observed that RTD has the best resistance-temperature linearity. The table compares three types of sensors: resistance temperature detectors (RTD), thermistors, and thermocouples.
It can be seen that RTD has a significant advantage in measuring temperatures at medium and low levels. For high-temperature measurements, thermocouples perform better. At certain temperatures, high-precision thermistors are more suitable.
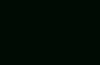
Although RTD has good linearity, to obtain relatively accurate temperature values, we typically refer to calibration tables.
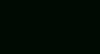
4.Measurement Method
Now that we understand the measurement principle of RTD, So how is RTD measured? When measuring resistance, we first think of using Ohm’s Law(R = U/I). When measuring resistances with relatively low values, a constant current source is commonly used as the excitation, and then the voltage across the resistance is measured to calculate its resistance value.
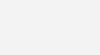
The maximum excitation current used for RTD is 5mA, so typically, 1mA or even smaller currents are used as the excitation. We will employ a three-wire PT100 thin-film resistance temperature detector (RTD) to measure the temperature of the mobile phone.
The exposed thermal resistance of PT100 thermometer is used in the experiment.
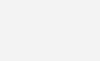
When measuring the temperature of some electronic components, the response time will be faster and more accurate.
The common thermal resistance is to insert the temperature measuring resistor into the stainless steel casing. This can protect the temperature measuring element.
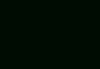
During temperature measurement, the sensing end of the RTD is placed in contact with the object being measured. We connect the RTD to the M2111 RTD temperature acquisition module and establish a connection to a computer through a 485 serial port converter. SDS1011 is connected to the computer. At the same time, SDS1011 can also supply power to the temperature acquisition module. This allows us to display real-time temperature data on the computer.
The figure above shows the connected setup.
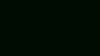
We then place the resistance temperature sensor near the mobile phone’s camera. After configuring the relevant parameters in the acquisition software, let’s begin the testwhile playing a game to observe.
How much the phone’s temperature increases during a game session.
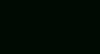
By inspecting the stored CSV file, we can view the temperature data collected by the sensor at each moment.
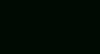
Returning to the waveform graph and zooming in on the y-axis, we can observe that the current phone temperature is 37.7°C, and its initial temperature was 32.4°C before starting the game. The game session lasted approximately 15 minutes. Based on this data, we can estimate that the phone’s temperature increased by approximately 0.35°C per minute during gameplay. However, please note that this is just an estimation, and various factors might not have been accounted for.
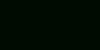